Blog
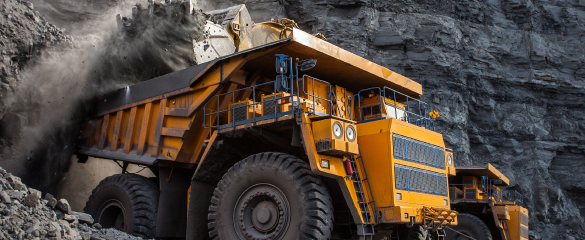
Leveraging Our Decades of Experience to Address Multiple Mining Modernization Challenges
Manual Grind Line Modernization
To improve site safety, increase output, and reduce operational costs, many mines are now looking to modernize manual, outdated, and obsolete systems. This was the case recently for a large magnesia mine in the US that was still operating its grind line manually. Since the mine was running each machine on the line locally and did not have a central supervisory control and data acquisition (SCADA) system in place, the process was inconsistent and not particularly safe for operators.
Even though the site knew it really needed to invest in modernization, like many mines, this site did not have a fulltime onsite engineer as one really was not required on a daily basis. However, without an onsite engineer, it was difficult to determine the status of the current system so that requirements for a new automated system could be developed. Therefore, it took several years to get the potential modernization project to a point where the site was ready to bring in a third party to assist. Since GTH engineers had already formed a relationship with this mine as we had built a few replacement panels and provided some OEM equipment and PLCs for other outdated control equipment onsite, it was a natural choice to bring us in as an engineering and system integration resource for this project as well.
At the beginning of this modernization engagement, we faced several challenges regarding how to determine the scope of work (SOW) for the modernization. Then, once the SOW was set, we designed the new system, but we ran into another distinct set of challenges as we incorporated the new modern and automated system into their manual process line.
To learn how our engineers solved these complex modernization challenges and the many benefits of this new modernized system, download the full case study – Modernizing a Manual Grind Line for a Remote Magnesia Mine.
GTH Phased approach to Large Control System Modernization
Over the years, we’ve seen many organizations shy away from modernization because they envision the project being performed as a rip and replace that requires a complete shutdown for many days or weeks. But at George T. Hall (GTH), we understand an extensive shutdown really is not an option for most facilities as lost production can be quite costly. Instead, we believe a well-planned phased approach to modernization is more practical.
We recently completed a project with a gold mine in Nevada when they determined it needed to modernize the PLC control system. While still operational, the hardware being used had reached the end of its commercial life. Additionally, availability of replacement parts and plant downtime was of significant concern. GTH partnered with Schneider Electric to develop a well-planned phased approach to modernization that represented the lowest risk with the highest value. GTH was able to prove that they could minimize all the potential risks that the customer was concerned about.
While many integrators have experience performing SCADA and PLC modernizations, not many companies have been around long enough to have extensive experience working with both legacy and modern systems. At GTH, we have many decades of experience serving as a platform-agnostic integrator and we are well-versed in working with a wide variety of software and hardware for PLC and SCADA systems. To learn more about the phased approach we took with the modernization and the benefits seen by this gold mine, download the full case study – Large Control System Modernization Gold Mine – Northern Nevada.
RELATED POSTS
Determining if your instrument is calibratable and when to consider an upgrade or replacement
In the rapidly evolving world of controls and automation, efficient design and manufacturing processes...