Blog
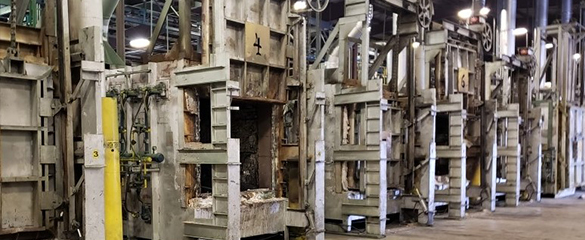
Budget-Friendly Tips to Boost Heat Treat Furnace Efficiency – Part 2
Tip 3: Ensuring Pressure Control Remains in Tune
To ensure proper furnace pressure is maintained, which means keeping the pressure inside the furnace as close to neutral as possible, or + 0.01” as measured on a water column, there are a couple of things you need to watch for. First, you need to be sure your flue is properly sized, and that the location of the flue is accurate based on the type of furnace you are using. For example, if the burners are mounted high on the furnace walls, the flue should be close to the floor to draw the hot gases down to the bottom.
It is also important to consider if you have, or will have to, convert from standard burners to low nitrogen oxide (NOx) burners to comply with newer environmental regulations. When a furnace is converted to use low NOx burners, there is usually an increase in the volume of excess air being pushed through the burner to lower the flame temperature and reduce the NOx emissions. The additional air volume passing through the furnace can increase furnace pressure, which means you will need to recalculate the flue area to confirm that it can handle the increase in excess air and adjust accordingly.
The next thing to look at regarding furnace pressure control is the location where the pressure tap enters the furnace to control the pressure (Figure 1). In general, the location of the pressure tap should be dependent on the material processed in the furnace, the location of the burners, and/or how the furnace is loaded.
Figure 1. A furnace pressure tap entering the furnace.
Additionally, since an extremely low positive pressure is needed for proper operation of a heat treat furnace, you should have a good reference for the pressure controller itself and remember to calibrate your pressure transmitter regularly. It is also worth mentioning, at this point, as part of ASM2750G instrument calibration sticker requirements slightly changed as well, and the furnace or instrument number must be identified on the sticker.
Our furnace specialists are available to assist you with reviewing your present furnace pressure control system to determine how to improve its repeatability. This can include providing an assessment of the proper range transmitter, finding the ideal location for the pressure to be measured at, as well as, determining if you are using the best option for a control device.
Tip 4: Upgrading Outdated Sensor Technology
While we understand upgrading older sensors is certainly not a no-cost option, changing out sensors is a very minor expense compared to the cost of replacing your heat treat furnace. Plus, depending on what the sensor was measuring, making these changes may offer significant cost savings that far exceed the cost of the sensor upgrade. Or, for some sensors, upgrading to a newer type of sensor may significantly reduce maintenance costs and downtime.
For example, one of the simpler furnace pressure control loops ON a heat treat furnace uses sensors that contain a potentiometer system to control process variables. Since the wiper rubs on the slidewire, there is a lot of friction, and they will typically wear out quickly. When replacing these units, we highly recommend taking the opportunity to upgrade to a newer contactless sensor option which will provide greater reliability and repeatability. Figure 2 shows the difference between a traditional mechanical sensor and a newer contactless sensor.
Figure 2. The sensor on the left is a potentiometer that uses a slide wire and wiper while the sensor on the right is a contactless option.
Get the Conversation Started: Improve Operations Without a Major Capital Expenditure
Just as many people take their method of transportation for granted when it is running smoothly as they do when they are not working as well as it did in the past. Many manufacturers ignore their heat treat furnace until production calls because it is not working properly. But ignoring your heat treat furnace until a problem arises can be a big source of inefficiency in your operations. By evaluating some of the preventative measures discussed in this two-part blog series and consulting with our team of furnace control specialists as needed, you may discover several low-cost, ways to bring more uniformity and reliability to your heat treat process, improving productivity and profitability.
RELATED POSTS
Fireye introduces the new BurnerLogiX Flame Safeguard with valve proving and low gas pressure...
How has climate change affected us locally?Like all other regions of the globe California has seen the...