Blog
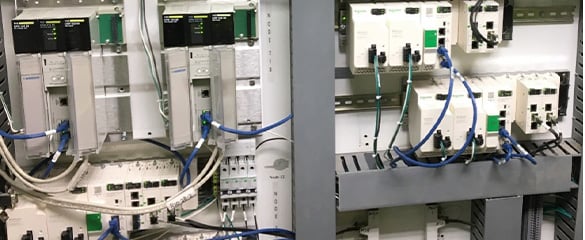
Three Ways to Reduce Risk During a Modernization
When organizations continue to run mature or obsolete supervisory control and data acquisition (SCADA) systems and programmable logic controllers (PLCs), there are a number of business risks they could be facing, including increased and/or extended downtime and a variety of cybersecurity vulnerabilities. However, the possibility of requiring downtime to execute a modernization, along with other perceived risks of moving to an updated system such as compatibility issues, prevent many companies from executing a much-needed modernization. This blog post shows how it is possible to minimize these types of risks by working with a highly qualified integrator to develop a customized, well-planned phased approach to modernization that capitalizes on your existing planned downtime.
Execute Your Modernization in Well-Planned Phases
Over the years, we’ve seen many organizations shy away from modernization because they envision the project being performed as a rip and replace that requires a complete shutdown for many days or weeks. But at George T. Hall (GTH), we understand an extensive shutdown really is not an option for most facilities as lost production can be quite costly. Instead, we believe a well-planned phased approach to modernization is a much more practical.
While we customize our modernization plans to meet the specific needs of each company we work with, let’s look at one example of how this works by reviewing a modernization we recently performed for a gold mining company. We engaged with this company when they decided they needed to modernize their 25-year-old PLC control system, which included 13 hot standby Quantum systems. From our initial conversations, we knew a multi-year phased modernization plan would be the most practical option for converting this legacy system to a modern system using Modicon M580 process automation controllers (PACs) and X80 I/O. An overview of the three phases of this project, and the allotted downtime we were required to work within, is provided in the table below.
Phase | Allotted Downtime | Overview of Work Completed |
Phase I – PAC Implementation and Validation | N/A |
|
Phase II – PAC Installation and Commissioning | 10 Days |
|
Phase III – I/O and Networking Upgrade | 15 Days |
|
Capitalize on Scheduled Downtime
Given that downtime can be extremely costly for most companies, it is best to capitalize on scheduled downtime to perform changeouts for a modernization. To do this, a modernization plan likely needs to include hybrid solutions designed to support old and new portions of the system simultaneously. In the example described above, when we provided our initial proof of concept, we had to demonstrate our understanding of the conversion requirements and the capabilities of the new software and hardware platforms. This included showing that we could complete the required work during their scheduled downtime windows and also that the hybrid systems in use between phases of the upgrade would not have compatibility issues. The hybrid system in place between phases II and III is shown below.
Select an Integrator with Proven Modernization Experience
While many integrators have experience performing SCADA and PLC modernizations, not many companies have been around long enough to have extensive experience working with both legacy and modern systems. At GTH, we have many decades of experience serving as a platform-agnostic integrator and we are well-versed in working with a wide variety of software and hardware for SCADA systems.
We also have developed proven methods and systems to help us further minimize downtime and risk during modernization implementations. For example, as shown above, a standard part of our modernization process is the extensive factory acceptance testing (FAT) we perform on our solutions. We also supplement this testing with extremely thorough documentation for all our systems. Additionally, we have a number of industry certifications and partnerships that provide our customers with early access to innovative technologies as well as higher levels of support. In this example, our status as a Certified Automation Partner with Schneider Electric gave us access to UMAC, which made it much easier and faster to convert from the existing PLCs to the modern PACs.
Overall, our engineers are well-versed in developing solutions that address the concerns and potential risks of modernization, allowing companies to experience the numerous benefits a modern SCADA system can offer.
Download our latest white paper to learn more about mitigating control system risks and inefficiencies with a well-planned phased SCADA modernization.
RELATED POSTS
Determining if your instrument is calibratable and when to consider an upgrade or replacement
In the rapidly evolving world of controls and automation, efficient design and manufacturing processes...