Blog
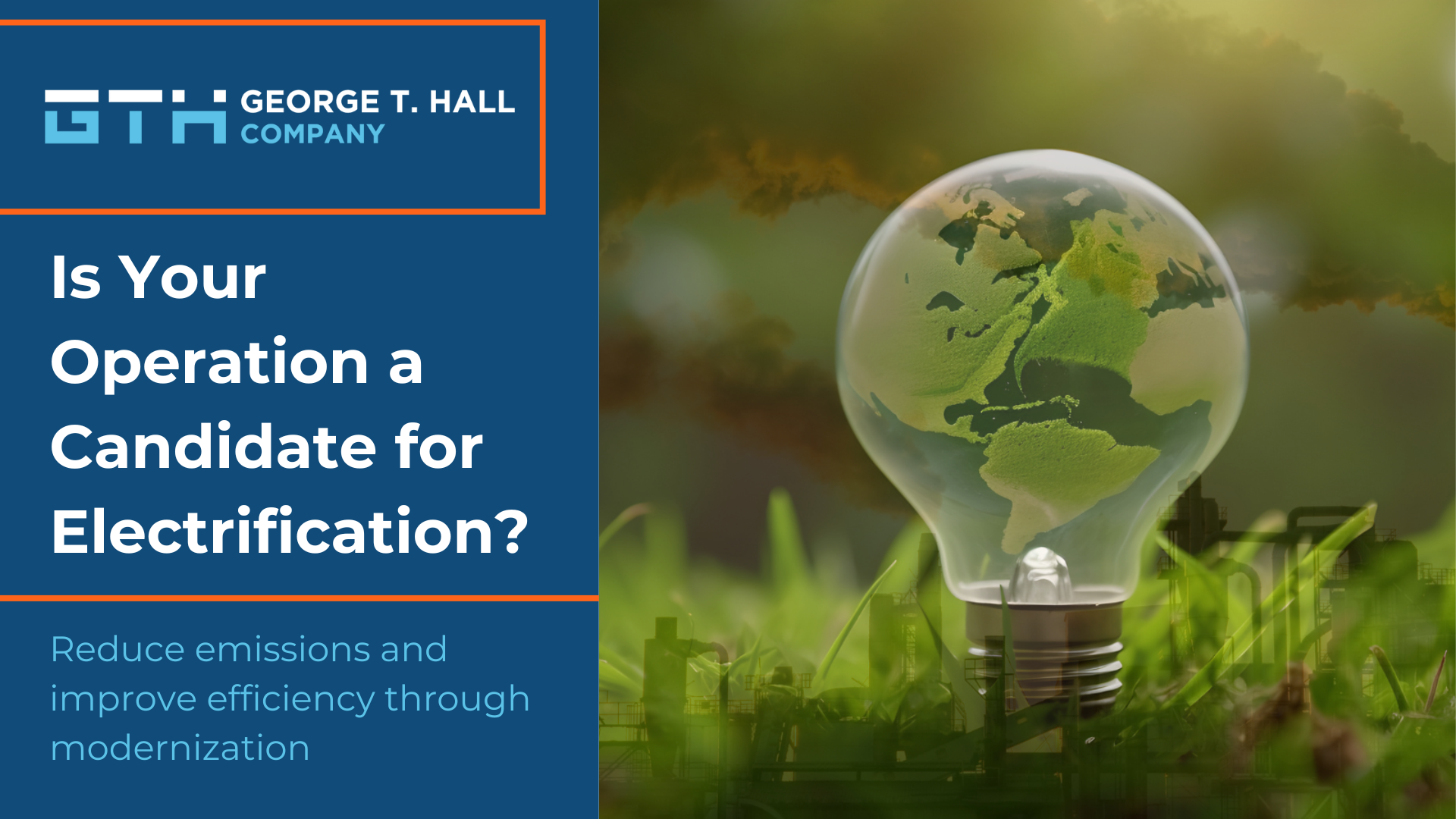
Is Your Operation a Candidate for Electrification?
Reduce emissions and improve efficiency through modernization
In a recent article published in Automation World, “How Electrification Can Help Manufacturers Achieve Sustainability”, we highlighted the potential of electrification to drive sustainability. We touched on ideal applications but now aim to delve deeper into the steps to identify if your operation is suitable for electrification and how to determine its viability for your processes.
With California’s aggressive carbon neutrality goals for industrial operations, many businesses are aligning their strategic plans to meet these targets. While not all states have adopted similarly ambitious goals yet, California often sets the standard, and current trends suggest other states will follow suit. Electrification presents a promising option for operations to meet these goals, but there are several factors to consider in determining whether electrification is right for your facility. In this article, we aim to guide you through the process of evaluating your operation’s suitability for electrification. Engaging with our Business Development Team throughout this journey will provide valuable support in making an informed decision about whether this upgrade is right for you.
Let’s take the first steps in understanding how your facility can begin the electrification process.
Getting Started
Step 1:
The first step in determining if your application is a candidate for electrification is to confirm its maximum operational temperature. Electrification is generally suitable for applications requiring temperatures not to exceed 1200°F. If your application exceeds this limit, electrification may not be appropriate.
However, if it operates at 1200°F or below, you can proceed to the next step in assessing whether electrification upgrades are suitable for your operation.
Step 2:
Now that you’ve confirmed your application’s maximum operational temperature is suitable for electrification, the next factor to consider is load variability. Electrification is most effective for processes with low and consistent loads. If your application experiences significant fluctuations, electrification may not be ideal.
To determine your system’s load variability, it’s important to collect specific data by using digital chart recorders such as the Eurotherm 6100A and 6180A Series Data Recorders. For more information on this specific recorder, click here and check out our past blog titled, “Evolving Regulatory Standards in Electronic Data Collection”.
By using digital chart recorders, we can measure the current gas flow and convert it to kilowatts, providing a comprehensive understanding of the power required for electrification. This data helps calculate the potential electrical load needed and informs the decision about necessary power system upgrades.
The key data points to gather include:
- Type of fuel currently used (natural gas, propane, etc.).
- Monthly fuel consumption (in BTUs).
- Historical fuel costs.
- Thermal efficiency of the current system.
- Age and condition of the existing system.
- Available physical space for equipment upgrades.
- Electrical power requirements (480V 3-phase or 230V 3-phase).
- Required temperature ranges for each process.
Once this data is collected and analyzed, you’ll have a clearer picture of whether your application has low and consistent load variability, making electrification a feasible option. You can then proceed to the next step in evaluating electrification upgrades.
Step 3:
After assessing load variability, the next crucial step is evaluating your facility’s electrical capacity. Electrification requires significant electrical power, which may necessitate upgrades to infrastructure such as transformers, switchgear, and breakers. Collaborating with our Business Development Engineering team will allow us to measure your facility’s current electrical capacity and your application’s required amperage. This evaluation will determine whether the existing infrastructure can support the increased load or if additional upgrades are needed.
In this step, we will assess the entire scope of potential upgrades required to transition your system to an electrical process. We will provide recommendations on the necessary equipment, such as Electric Heaters, SCRs, Controllers, Chart Recorders, and various other components required to support your specific application. Additionally, this evaluation enables us to make precise recommendations for power system upgrades, ensuring your infrastructure is prepared for electrification.
Ultimately, this step will allow us to make the final determination on whether your system is suitable for an electrification upgrade, ensuring that all components of the facility are capable of supporting the new electrical load. By the end of this process, we will be in a position to clearly outline what upgrades are necessary and the equipment best suited for your application’s needs.
Evaluating Cost and Long-Term Benefits
Now that you’ve determined your application is a candidate for electrification, what’s next? The next step is performing a cost analysis to evaluate when this type of upgrade fits within your budget. We understand that many operations hesitate to take action on electrification upgrades due to the significant upfront costs. However, it’s important to remember that while the initial investment can be substantial, the long-term benefits often outweigh the costs. Some key advantages to consider include:
- Reduced maintenance overhead due to fewer moving parts, resulting in increased operational efficiency and lower long-term costs.
- No AQMD source testing required, as electric equipment produces zero emissions.
- Government incentives available.
- Alignment with carbon neutrality initiatives, supporting California’s goal of achieving carbon neutrality by 2045.
During the steps outlined above, we made recommendations on the necessary equipment and infrastructure upgrades for electrification. With this information, you can strategically plan the timing of your investment. While the upfront costs are a consideration, the long-term gains can position your operation for future growth and sustainability.
Now that you’ve assessed your facility’s suitability for electrification and identified your budget, partnering with a System Integrator like GTH is crucial to successfully implementing the upgrade. In the next section, we’ll explore why GTH is the right choice to guide you through this transformative process.
For nearly a century, George T. Hall Company has been at the forefront of control solutions, offering a comprehensive suite of services that span the entire electrification process. As a full-service provider, we combine technical expertise with practical support, ensuring your operation can transition to electrification smoothly and effectively. From the distribution of components like graphic and paperless recorders, which are essential for accurate data collection, to our on-site field services that troubleshoot and optimize your systems, we are committed to providing end-to-end assistance.
Our decades of experience within the thermal and process industries give us unparalleled insight into both legacy and modern heat treat processes. We understand the intricacies of your systems and are well-equipped to guide you through the complexities of electrifying them. We are proud to partner with Watlow-Eurotherm, the global leader in electrification technology, whose significant investment in research and development has positioned them as the premier manufacturer of systems designed to replace outdated gas-run applications.
The collaboration between GTH and Watlow-Eurotherm is integral to executing a successful electrification upgrade. Our expertise, combined with cutting-edge technology, ensures that your systems are not only modernized but optimized for efficiency and sustainability.
Additionally, GTH is a CSIA-certified system integrator, certified to ISO 9001:2015 by DQS, and was named Hall of Fame System Integrator of the Year for 2023. Our certifications and accolades underscore our commitment to excellence in thermal and process control solutions. With this depth of experience and a proven track record, we are uniquely positioned to help you achieve a seamless transition to electrification, providing lasting value to your operation.
Electrification may not be the right solution for every application, and the upfront costs can be significant. However, as industries face increasing environmental regulations and the push for carbon neutrality, adopting electrification is becoming an essential consideration for long-term sustainability and compliance. The decision to electrify is not just about meeting current needs but positioning your operation for future success in a world of evolving standards and environmental responsibility.
As a full-service control solutions provider, GTH is here to guide you through every step of the process. Click here to contact one of our experts.
Resources for government incentives:
Qualifying Advanced Energy Project Credit (48C) Program
Credits and Deductions under the Inflation Reduction Act of 2022
Tax Guide for Green Technology
Check out GTH in Automation World with our latest article, "How Electrification Can Help Manufacturers Achieve Sustainability".
RELATED POSTS
How has climate change affected us locally?Like all other regions of the globe California has seen the...
In the first part of this blog series exploring budget-friendly tips to improve the efficiency of your...