Blog
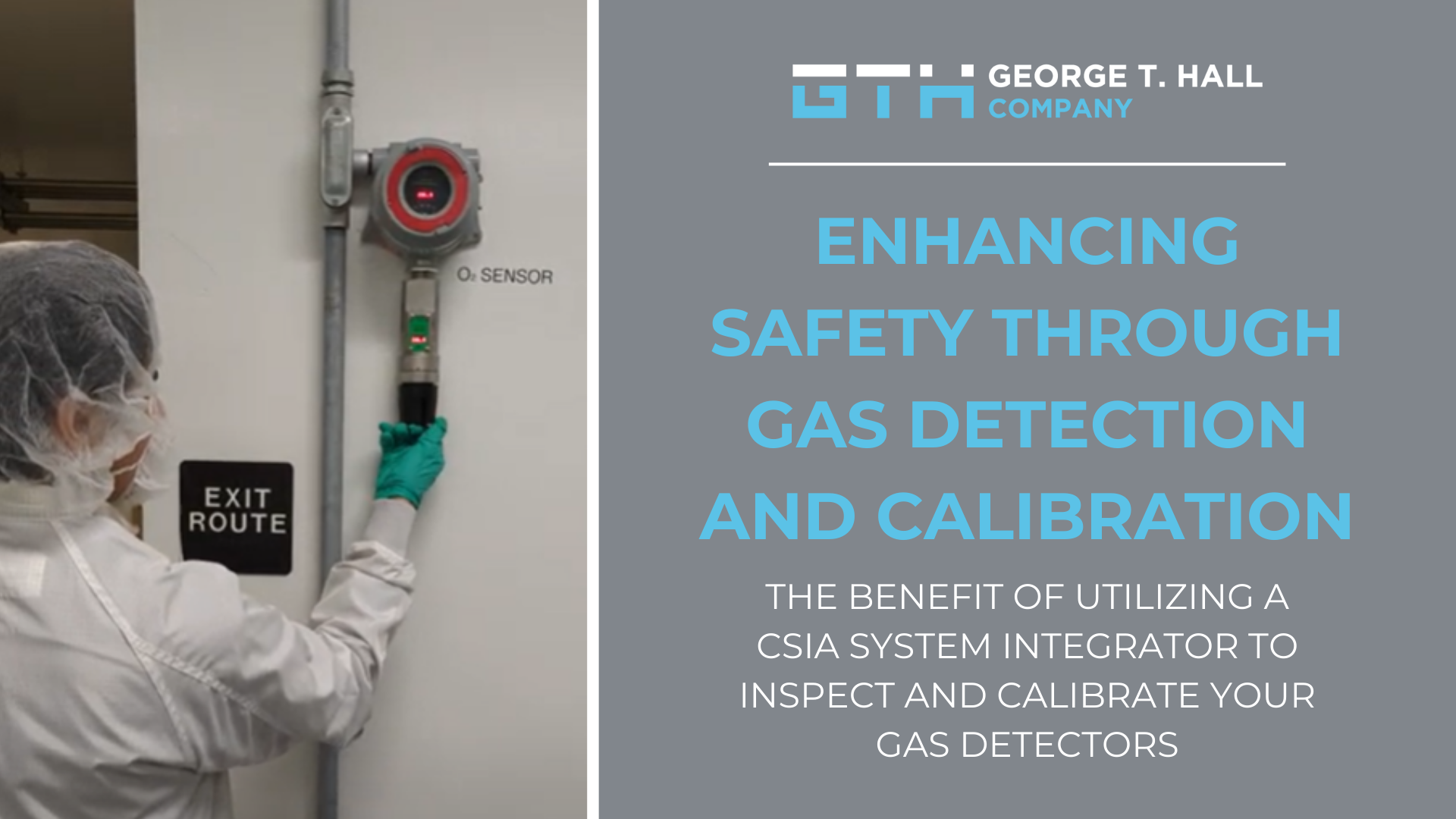
Enhancing Safety Through Gas Detection and Calibration
Safety is paramount for all industrial operations; ensuring the well-being of personnel, protecting the environment, and maintaining proper facility functioning are top priorities. Gas detection and calibration play pivotal roles in achieving these objectives. In this blog, we delve into the significance of gas detection, the role of gas sensors in environmental safety, the calibration process for gas detection units, and the importance of LEL standards and calibration in industrial operations. Furthermore, we explore the potential benefits of outsourcing calibration and engineering solutions to a third-party system integrator, like George T. Hall (GTH).
Within the world of pharmaceutical production, precision is crucial and chemical reactions are as delicate as they are complex, the stakes for safety have never been higher. Pharmaceutical Manufacturers navigate through intricate processes, from mixing and granulation to milling and coating, to ensure the precise formulation of life-saving compounds. Yet, hidden within these processes lie potential hazards that, if not meticulously monitored, could pose serious threats to the safety of those working in the production facility.
As we explored in our previous blog on "Reducing Safety Risks in Pharmaceutical Operations," the journey of pharmaceutical production is riddled with challenges, especially when it comes to handling raw materials, solvents, and the intricate dance of chemical reactions. While the industry comprehends the gravity of life safety risks, finding effective solutions to monitor these invisible threats can be a daunting task. With nearly a century of experience working across all key infrastructure industries such as Pharmaceutical, Water & Wastewater, Mining, and more, our customers rely on GTH’s for our expertise within gas detection and calibrations to enhance safety. Drawing on our wealth of knowledge, we present proven recommendations for automated monitoring and control solutions to fortify employee safety in the face of potentially hazardous materials.
In this blog, we pivot from the pharmaceutical realm to the broader landscape of industrial operations, focusing specifically on the critical roles of gas detection and calibration. As we delve into the intricate world of gas detection, we'll explore how the right sensors can safeguard not only pharmaceutical facilities but also various industrial environments where invisible gases pose a constant threat. Just as GTH has assisted pharmaceutical facilities in identifying and mitigating risks, we'll showcase how our expertise extends to gas detection solutions, ensuring that your production space remains a haven of safety. From the installation of combustible gas sensors to the integration of a comprehensive gas monitoring system, our proactive approach aims not just to detect hazards but to prevent them. Navigate the intricate landscape of gas detection, calibration, and proactive safety measures in industrial operations with us. Let George T. Hall be your trusted partner in ensuring that your facility doesn't just meet safety standards but exceeds them. Safety isn't just a priority – it's our commitment.
Gas Detection
In industrial operations, the management of various gases from production processes is crucial. Understanding and monitoring gases like methane (CH4), hydrogen sulfide (H2S), carbon dioxide (CO2), and ammonia (NH3) are imperative. Gas detection instruments, ranging from fixed detectors to portable devices and area monitors, utilize sensor technologies like electrochemical, paramagnetic, chemiluminescence, infrared, and catalytic bead sensors. Visual and audible alarm systems trigger at specific concentration levels.
Best practices in gas detection involve personnel training, regular maintenance, integration with safety protocols, strategic sensor placement, and the implementation of continuous monitoring systems for real-time alerts. Gas sensors play a pivotal role in safeguarding the environment and human health in industrial operations. Early detection of hazardous gases, monitoring workplace air quality, and contributing to air quality assessments are key functions. Gas sensors are integral to environmental protection, emissions control in industrial processes, manufacturing monitoring, and emergency response. They aid in preventing fire and explosion hazards, provide data for environmental policies, and contribute to continuous monitoring through remote sensing applications.
Calibrations
Calibrating gas detection units is vital for accuracy in industrial operations. Calibration involves using certified calibration gases with known concentrations and adjusting instruments to match these concentrations. The process includes steps such as zero calibration, span calibration, and recording calibration data. Calibration frequency depends on factors like sensor type, manufacturer recommendations, and environmental conditions. Proper calibration ensures instruments provide reliable readings, preventing false alarms and contributing to emergency response preparedness.
LEL standards, defining the lowest concentration of a flammable substance that can ignite, are vital for safety in industrial operations. These standards ensure the safety of personnel, compliance with regulations, proper facility design, risk assessment, and effective hazard mitigation. Calibration, on the other hand, ensures the accuracy of gas detection instruments. Properly calibrated instruments reduce liability, support compliance with standards, and enhance emergency response preparedness.
The frequency of calibration, determined by sensor type, environmental conditions, and manufacturer recommendations in industrial operations, includes daily bump tests and periodic calibrations. Manufacturers provide guidelines in user manuals, online resources, and may offer service plans. Adhering to these recommendations ensures instrument accuracy, reliability, and compliance with regulatory requirements. Regulatory agencies enforce specific standards governing diverse manufacturing processes, encompassing the production and storage of materials.
Utilizing a CSIA System Integrator to Inspect and Calibrate Your Gas Detectors
Choosing a CSIA Certified System Integrator such as George T. Hall to handle calibrations and provide high-quality engineering solutions for your operation yields numerous benefits. This includes tapping into the specialized knowledge and expertise of GTH engineers and technicians dedicated to calibration and system integration. By doing so, you can ensure strict adherence to industry standards and regulations without the need for in-house expertise. Streamlining your operations becomes possible through the outsourcing of non-core functions, allowing your team to concentrate on core competencies. This approach not only enhances efficiency but also eliminates the upfront costs associated with equipment and personnel training, opting instead for a cost-effective outsourcing model.
Our commitment extends to delivering reliable calibration services tailored to meet your specific process and quality requirements. Utilizing NIST-traceable instruments, we perform gas, temperature, pressure, and level calibrations across a range of industrial instruments. From Chart/Video Recorders, Controllers, Transmitters, Temperature Sensors, Gas Analyzers, Flow Meters to Humidity Instruments and Gauges, our comprehensive services cover various equipment. We ensure compliance with ISA standards when required, and our team includes refinery-trained field personnel with MSHA certification for mineral and mining applications. This comprehensive approach guarantees the precision and reliability of our calibration services for your operational needs.
Gas detection and calibration are integral components of safety management within industrial operations. By understanding their importance, following best practices, and considering outsourcing to a third-party system integrator, like GTH, decision-makers can enhance safety, compliance, and operational efficiency in their facilities.
For more information on our expertise, contact us.
RELATED POSTS
Since the inception of the George T. Hall Company (GTH), our founder, George Hall coined the phrase ...
What is New in the Updated AMS2750F? The AMS2750 specification covers pyrometric requirements for...
The Watlow F4T with INTUITION temperature process controller has a wide range of field removable I/O...